Product Circularity
Conserving Natural Resources and Managing Waste Responsibly
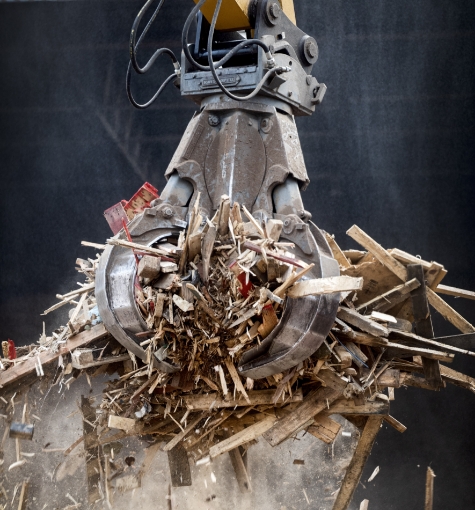
Manufacturing Waste Efficiency
Manufacturing processes inherently produce waste, but the most sustainable manufacturers understand that waste does not have to go to landfill and can instead be given a second life as a raw material in new products. Beyond the possibilities of reusing waste, it is also important to find ways to create less waste through leaner production processes.
Our journey to reduce waste-to-landfill began in 2010, when we set our first goal of reducing waste-to-landfill intensity. Through an intense focus on process efficiency, we achieved this goal in 2015, ten years early and continue to make progress.
We take a progressive reduce/reuse/recycle approach to waste reduction. For example, upgrading to more efficient equipment may allow a facility to generate less waste during a manufacturing process. Next, we look to reuse, either within a plant or across Mohawk divisions.
After reductions and opportunities for reuse are exhausted, we aim to divert waste from landfills through commercial recycling streams and the sale of waste to other businesses. Wherever possible, we try to keep our waste diversion local, identifying businesses near each facility with which we can partner and thus avoid additional transportation-related emissions.
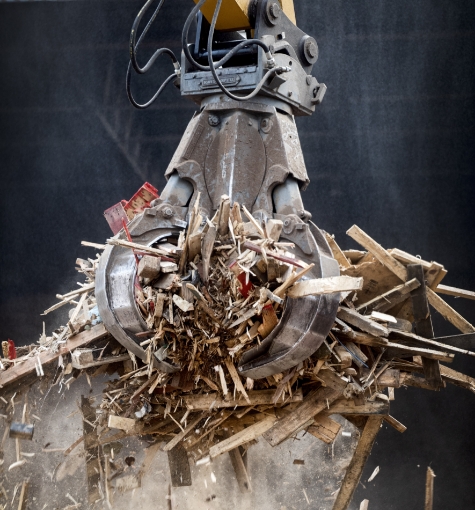
Water Restoration
Water is an essential manufacturing element of all flooring products. To make efficient use of this resource, Mohawk’s manufacturing facilities are taking steps to limit the amount of water we use and ensure that wastewater is managed in sustainable ways. Currently, we are working to reduce water intensity by 30% by 2025 against a 2010 baseline.
We have completed a water risk and stress assessment utilizing the World Resources Institute’s Aqueduct and the World Wildlife Fund’s Water Risk Filter tools. The outcome of this work will be available in our 2024 CDP Water Security Questionnaire.
Although we did not find water to be a material topic as part of our double materiality assessment, as part of our circular product approach, we continue to actively reduce water usage in our manufacturing processes and find improvements across the company that will ensure conservation of this resource. We have reduced water use in HVAC systems and created online tools to monitor water use. Mohawk has also developed new carpet fibers that are less water-intensive to manufacture than traditional yarns and use zero water in the dyeing process—using an average of 56% less water than competitive products.
1.In North America ceramic tile facilities, 84% of all process wastewater is recovered, with six of 11 plants successfully reusing 100% of their process wastewater.
2.In Belgium, we have established a closed-loop flow system with water sourced from a local river, contributing to a 40% reduction in process water use over the last decade.
3.In Italy, our ceramic tile plants not only achieve zero wastewater discharge but also actively recycle water from other ceramics manufacturers.
4.In Australia, we have implemented a “closed wash line” for latex application, which reuses water in the process, saving 600 liters of water per 14-ton latex batch.
5.At Grupo Daltile in Mexico, 100% of process wastewater is recycled and is classified as industrial water for consumption in the manufacturing of products and cleaning of equipment.
6.In North America, Mohawk Group’s patent pending Color PulseTM fiber technology eliminates water use in the dyeing process.
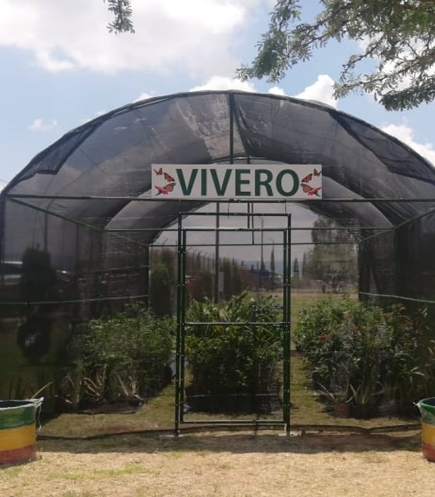
Grupo Daltile’s Vitromex ceramic tile plant in San Luis Potosí, Mexico, implemented a project to restore the 848-square-meter natural area surrounding the site, which had been degraded by mining. Reforestation efforts included planting aloe vera, mesquite and cottonwood trees. They also established an orchard with a variety of fruit trees, which further revitalized the area.
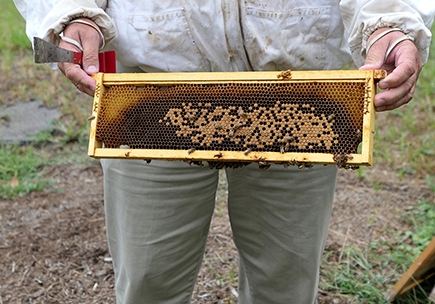
At our “Living Site” carpet tile plant in Glasgow, Virginia, Mo-Honey is a longstanding initiative that maintains on-site beehives to help preserve natural pollinators.
Biodiversity
Responsible sourcing of natural materials is a crucial part of our sustainable practices, enabling us to help preserve forests, safeguard biodiversity, support local communities and mitigate climate change.
Although biodiversity was not determined to be a material topic through our recent double materiality assessment, we continue our commitment to source our largest biological material—wood—responsibly. This includes ongoing work for all manufacturing locations adhering to wood sourcing principles, such as the Forest Stewardship Council (FSC®), the Programme for the Endorsement of Forest Certification (PEFCTM) or other third-party validation, toward our goal of ensuring 100% of the wood fiber in our products comes from responsibly managed forests, recycled waste streams or recovered wood sources by 2030.
In Europe, the wood in our laminate floors complies with the EU Timber regulation 995/2010 and is certified by recognized organizations like the FSC or other validated methods, ensuring sustainable and compliant sourcing practices. In Australia, our flooring products have obtained certification from the PEFC. We also use external auditing services to ensure wood is sourced according to U.S. Lacey Act requirements.
Mohawk Brasil is proactive in counteracting the environmental impact of its ceramic tile business by restoring natural habitats affected by clay extraction. In one project, around a kaolin mine, the company addressed soil acidity using limestone and introduced an organic substrate, resulting in rapid vegetation growth. Another initiative reclaimed a degraded area with cellulose biomass infusion, enhancing soil fertility and supporting diverse species.
In addition, Grupo Daltile’s ceramic tile plant in San Luis Potosí, Mexico, implemented a project to restore the 848 m² natural area surrounding the site, which had been degraded by mining. Reforestation efforts included planting aloe vera, mesquite and cottonwood trees. They also established an orchard with a variety of fruit trees, which further revitalized the area.