Product Circularity
At the heart of our approach lies a deep commitment to resource stewardship, encompassing elements such as biodiversity, responsible water usage and minimizing production waste every step of the way. We recognize that the product life cycle, from procurement to disposal, plays a crucial role in minimizing our environmental footprint. With a focus on waste diversion and thoughtful end-of-life philosophies, we are making progress toward defining and releasing a product circularity goal for each business by 2025.
MAKE
Innovate regenerative products through thoughtful design and efficient manufacturing that optimizes material use and expands post-consumer and sustainable content to minimize our products’ full life-cycle impact. Learn more
USE
Ensure product life is extended through superior performance and durability. Educate end-users about post-life-cycle options for reducing environmental impact. Learn more
RECOVER
Reclaim materials for a second and subsequent purpose after an initial, useful life. Learn more
Advancing the Circular Economy
We have reshaped sustainability in both residential and commercial spaces by prioritizing recycled and renewable materials in our products. Our approach minimizes environmental impact while ensuring functionality.
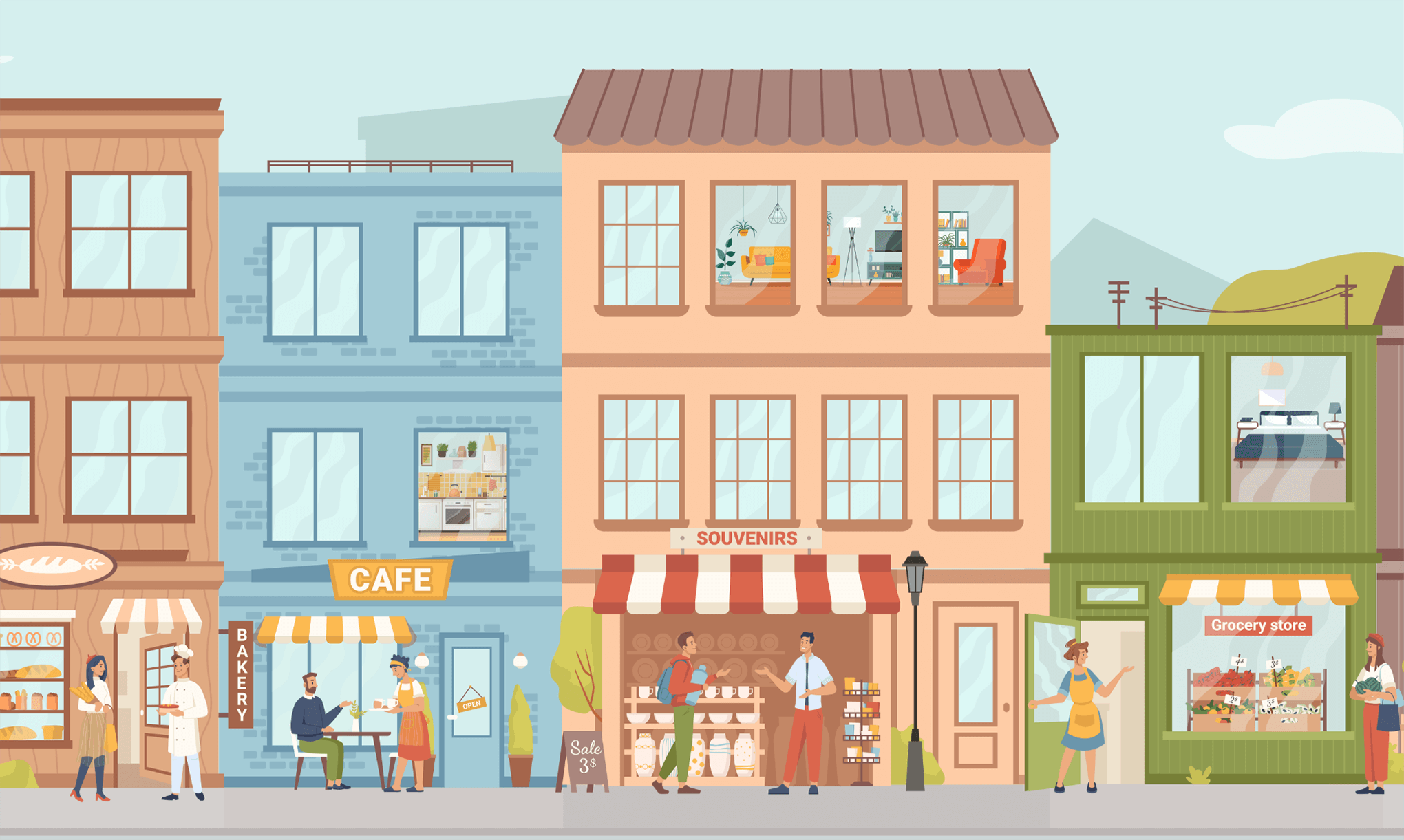
1.Unilin Group recycles 900,000 metric tons of waste wood into chipboards each year.
2.Luxury Vinyl Tile (LVT) manufactured in a closed-loop facility consists of 100% post-industrial recycled content.
3.Our new renewable polymer core (RPC) product, PureTech, offers a PVC-free alternative to resilient flooring while maintaining the waterproof capabilities and exceeding the scratch resistance of traditional luxury vinyl tile (LVT).
4.Unilin is the first business to recycle MDF and HDF material to produce new boards through patented recycling technology.
5.Mohawk Home annually recycles more than 40 million pounds of tires into decorative door mats.
6.At its facility in northeastern Brazil, Eliane produces ceramic tile using lime mud—a natural residue from a nearby cellulose manufacturing plant.
7.Unilin recovers raw materials from insulation boards, converting polyurethane back into building blocks for new boards.
8.Our exclusive SmartStrand carpet fiber (triexta) is made in part from bio-based material and is inherently stain resistant and durable.
9.In the U.S., Mohawk Home converts waste carpet fiber into non-woven rug pads for extra cushioning.
10.EverStrand and EnviroStrand carpet fiber are made from recycled PET plastic bottles using our state-of-the-art Continuum process, averaging more than 6 billion bottles each year.