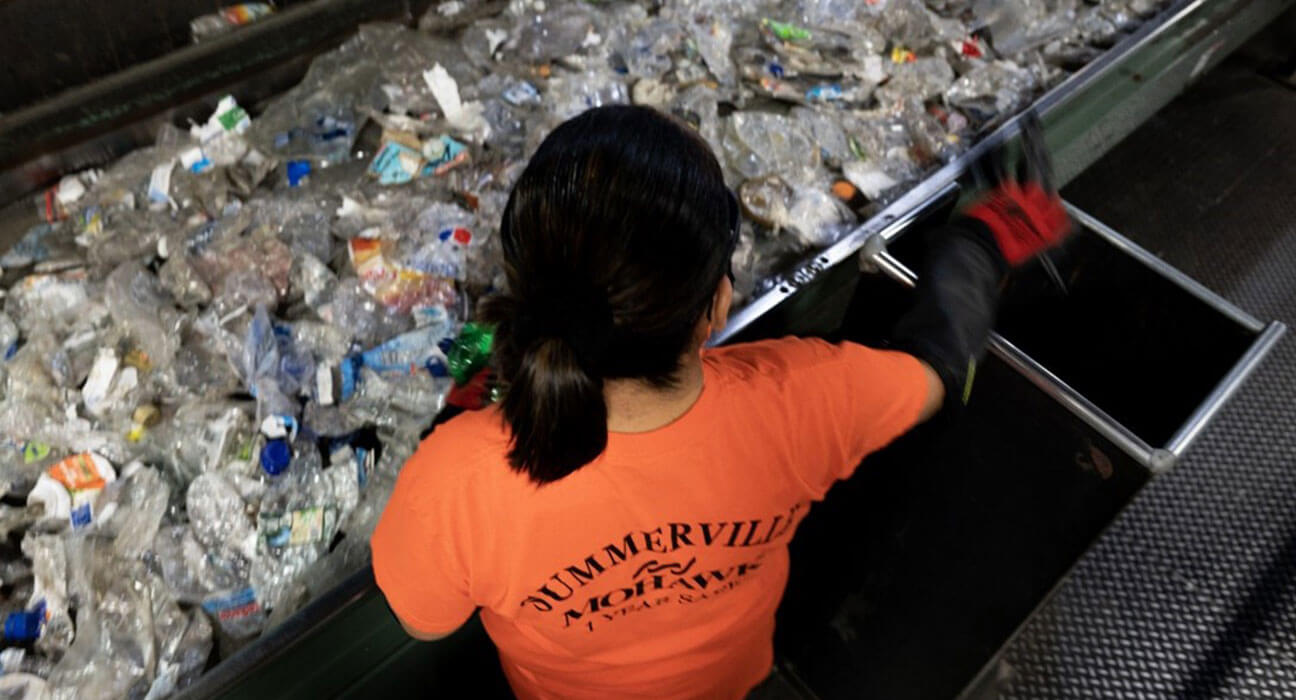
Summerville’s Recycle and Extrusion Facility
They Make What? Series
You may have heard that Mohawk is the world’s largest recycler of single-use plastic bottles, but did you know our Summerville facility is where it all takes place?
“On behalf of all Summerville associates, we are pleased to be recognized for our contributions to Mohawk’s soft surface business and the company’s world-class sustainability efforts,” said VP of Recycling Mark Dye. “Summerville is the largest integrated post-consumer polyester operation in the world, processing up to 7 billion bottles per year.”
The Summerville facility is split into 2 separate plants: Recycling and Extrusion.
The process starts when discarded plastic bottles are brought into the facility in large bales. A large drum is used to break the bottles apart, then the bottles are sent down a conveyor to be sorted. The Sort team makes sure any bottles that aren’t made of polyester are removed from the process and then the bottles are separated by color. Clear bottles can be used for all colors of carpet, and tinted bottles are used for darker dyed products.
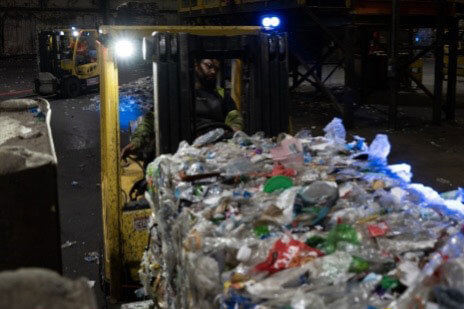
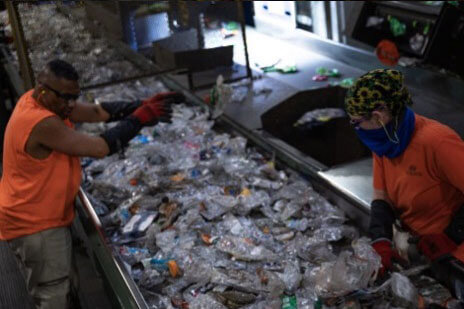
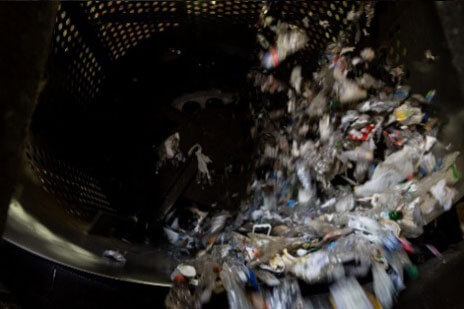
From there, the bottles go through an extensive cleaning and sanitation process to remove contaminants and get ground into small flakes, which are washed again, then sent to the Extrusion operation.
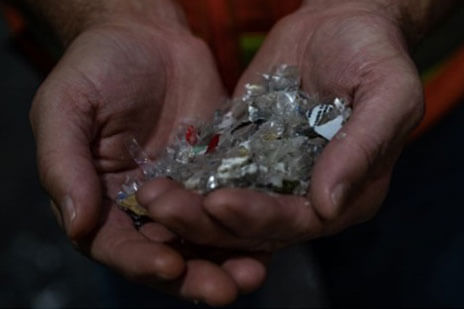
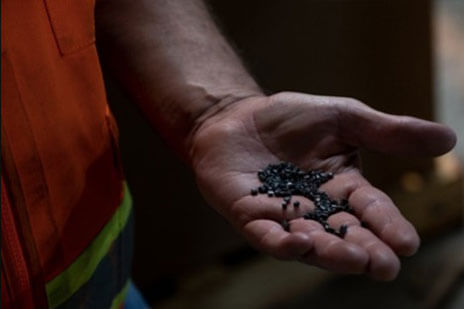
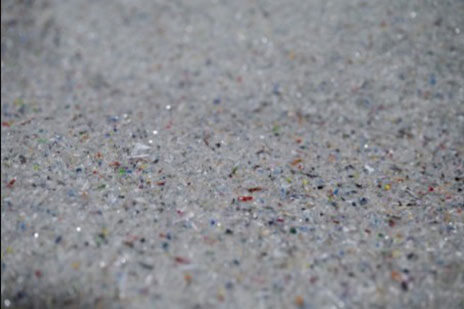
“Summerville’s Recycling team uses a variety of advanced technologies to convert post-consumer polyester bottles into polymer which is then used in Mohawk’s BCF extrusion and backing operations. We use stringent processes to refine and clean the recycled materials to ensure our finished products are of the highest quality,” said Sr. Plant Manager Jimmy Tapp. “We are particularly proud of the investments we continue to make to create a safer environment for our team members. We’ve already seen our investments pay off in a big way with a significant reduction in work-place injuries.”
When the Extrusion team gets the material, they are melted down and pumped through small holes to create the fiber, which is then put through a number of processes before eventually becoming the yarn to make soft surface products.
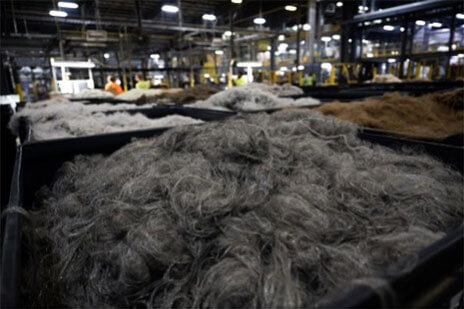
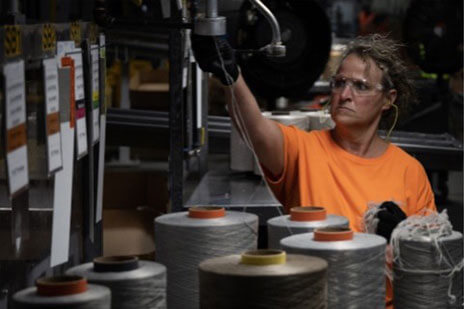
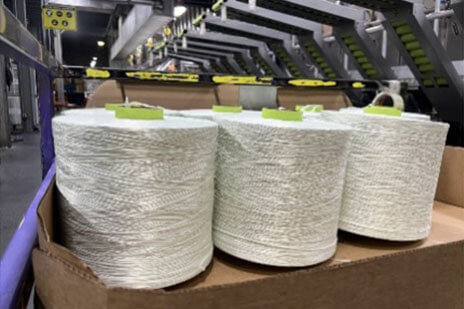
“Summerville’s BCF Extrusion team utilizes the polymer prepared in Recycling to produce a wide variety of polyester fibers for Mohawk’s carpet business. The team also utilizes a bio-based polymer to produce a portfolio of fine dpf TriextaTM fibers for high-end carpet applications,” said Plant Manger Rick Chelsey. “Summerville’s BCF plant is one of the industry’s largest and most versatile fiber extrusion operations. Like the Recycling team, BCF has made tremendous progress through investing in keeping our associates safe at work. In fact, we have currently worked over 350 days without an OSHA recordable injury. We are also proud of expanding our operational capabilities to support the company’s solution dye fiber strategy.”
Shoutout to the entire Summerville team for all they do to support Mohawk’s sustainability efforts and produce the materials used to make our exceptional soft surface products!